Smart warehouse, surely no stranger to manufacturing enterprises, is known as an automation solution that integrates many modern technologies, including Automated Guided Vehicle (AGV). With the ability to optimize efficiency in warehouse management, reduce human labor and increase work productivity, the AGV is currently an effective assistant for a smart warehouse.

What is an Automated Guided Vehicle (AGV) to transport goods in a smart warehouse?
An Automated Guided Vehicle – AGV is essentially a robot that moves thanks to guidance technology, which is applied in the logistics field, especially in a smart warehouse. In the process of moving, the AGV robot supports the transportation of goods between different areas of the smart warehouse by carrying or dragging a significant volume of goods, to help manage the warehouse efficiently, and improve the productivity of the operation operating in logistics.

Goods can be loaded in trolleys, crates to be pulled or lifted, can also be loaded onto the AGV itself, which has a built-in tray or roller conveyor, PVC conveyor depending on the required features. The AGV robot can also be a forklift with integrated automatic lifting, lifting pallets, rolls, crates or boxes. Sometimes the AGV system is a combination of robocar and collaborative robot (cobot) with the ability to pick up and place queues for pick & place applications.
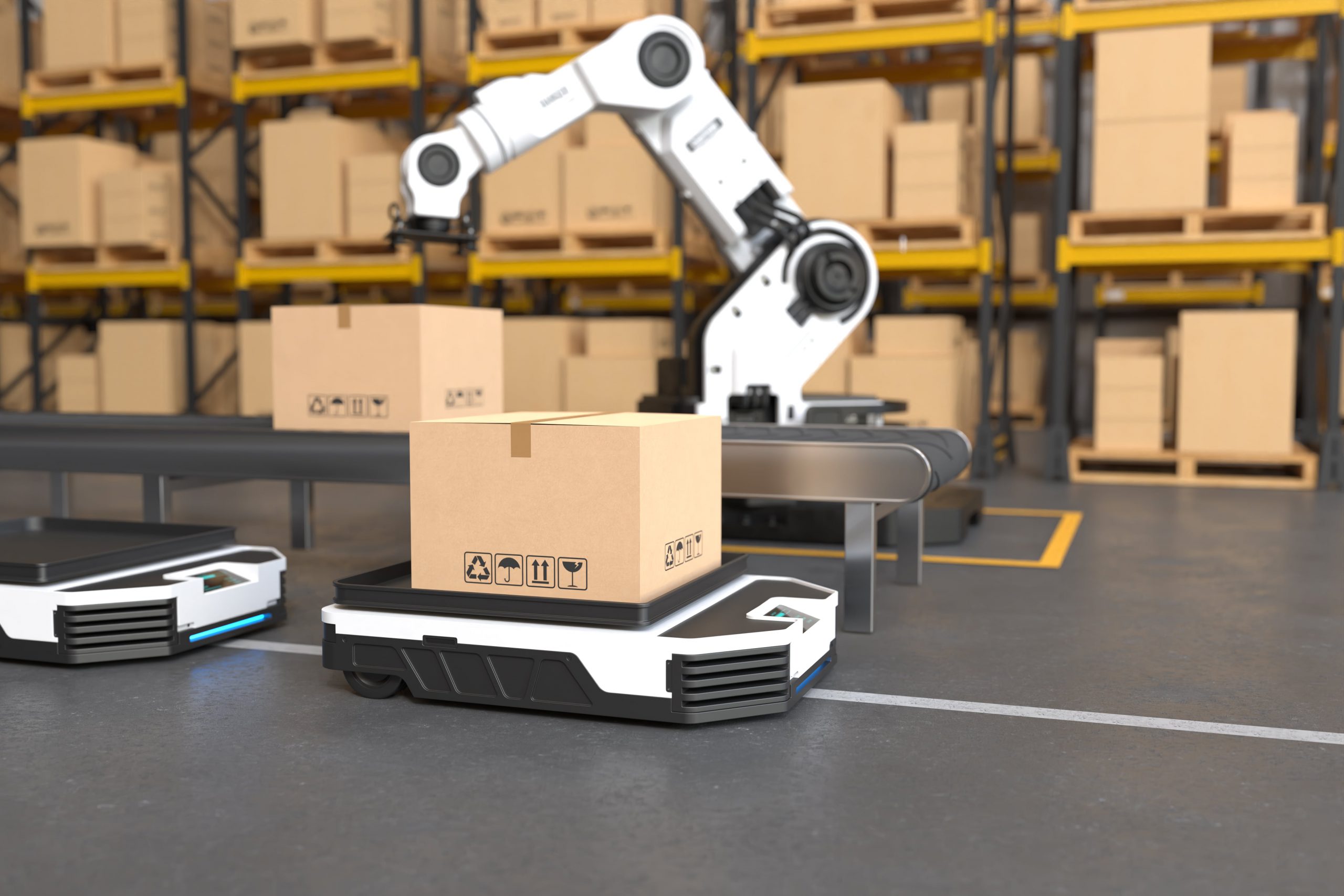
These AGV robots are a flexible automation solution, a powerful assistant in a smart warehouse replacing traditional forklifts for loading and unloading trucks, connecting storage areas with production lines and even moving products between different picking areas. Furthermore, the AGV is programmed to integrate with warehouse management software WCS, WMS, and even integrated with IIoT – that is, handling all warehouse-related operations via the internet connection.
Why is AGV an effective assistant for a smart warehouse?
Today, more and more businesses are actively promoting the deployment of AGV robots in the warehouse area, especially in the smart warehouse system towards building a smart factory, because of the outstanding benefits it brings:
1. Improve accuracy & increase productivity
With the use of an automated guided vehicle (AGV) in the automated warehouse area, logistics staff can easily handle a larger volume of goods in and out of the warehouse along with higher accuracy. The access to technology in the above transportation sector brings productivity and efficiency up to 30% higher than the previous use of human power. As a result, the smart warehouse can achieve faster order fulfillment, resulting in higher customer satisfaction.
2. Increase the safety for warehouse staff
The AGV vehicle creates a safe work environment with safety features that eliminate accidental collisions and damage to transport due to driver error.
The AGV system offers a safe and cost-effective alternative to the manual transportation of sensitive or hazardous products. The AGV robot is especially suitable for applications in a smart warehouse in harsh environmental conditions, such as cold storage.
The AGV robot works safely and effectively with humans. As the onboard sensors identify humans or machines in their path, the AGV will first slow down and then stop, depending on the distance to the subject.
3. Automate repetitive, manual tasks
The collaboration between a smart warehouse and AGV robot has helped logistics operations as well as businesses solve repetitive, manual work problems such as picking and transporting items around the warehouse floor. Now, employees can be optimally allocated to focus their time, energy and energy on handling more complex tasks, creating more value for the business.
It can be seen that the investment cost of an AGV robot can be relatively large, however, the effects that businesses receive are undeniable.
4. Save operation cost
Applying the AGV system in a smart warehouse will help allocate resources more efficiently, thereby reducing labor costs, along with other costs. With the ability to work flexibly and continuously 24 hours a day for many years, AGV robots will significantly shorten transportation time, save investment costs for other fixed automatic transportation systems such as conveyors, conveyor belts, etc. As a result, the productivity and operational efficiency of the factory can be increased by 20% or more, giving businesses a higher profit value.
Guidance technology for an automated guided vehicle
With increasingly high automation technology, AGV robots are programmed to automate with many different navigation technologies, depending on the needs of each business, there will be appropriate technology options to optimize productivity and investment costs.

1. Laser target navigation
- The AGV is equipped with a rotating laser that allows it to detect reflected objects inserted in its environment and establish its position very precisely.
- They are very precise and allow the product to be handled to the nearest quarter of a centimeter.
2. Wire guide technology
- The AGV moves along a track in the ground that may consist of a wire, track, magnetic field line, or cable.
- However, the AGV robots need to be engineering programmed to follow the rails to use this technology.
- For applications that do not require flexibility, this will be a suitable AGV technology.
3. Vision guidance
- The AGV system operates by using cameras to record features along the route, allowing them to replay the route by using the recorded features to navigate.
- Installation costs are lower than wire guides and this type of AGV does not require any special installation work.
4. Geoguiding technology
- This technology allows the AGV robot to detect and identify columns, stationary obstacles and walls in the smart warehouse. Using these fixed references, it can position itself, in real time, and calculate its trips automatically.
- This technology is very flexible as the AGV’s maps can be modified at any time by working directly on the mapping software.
- This is the most reliable solution.
Applications of AGV robot in a smart warehouse
In an automated warehouse, AGV is used in logistics tasks. Businesses use AGV robots to transport goods and products from one location to another. Let’s take a look at some popular applications of AGV robot in a smart warehouse, including:
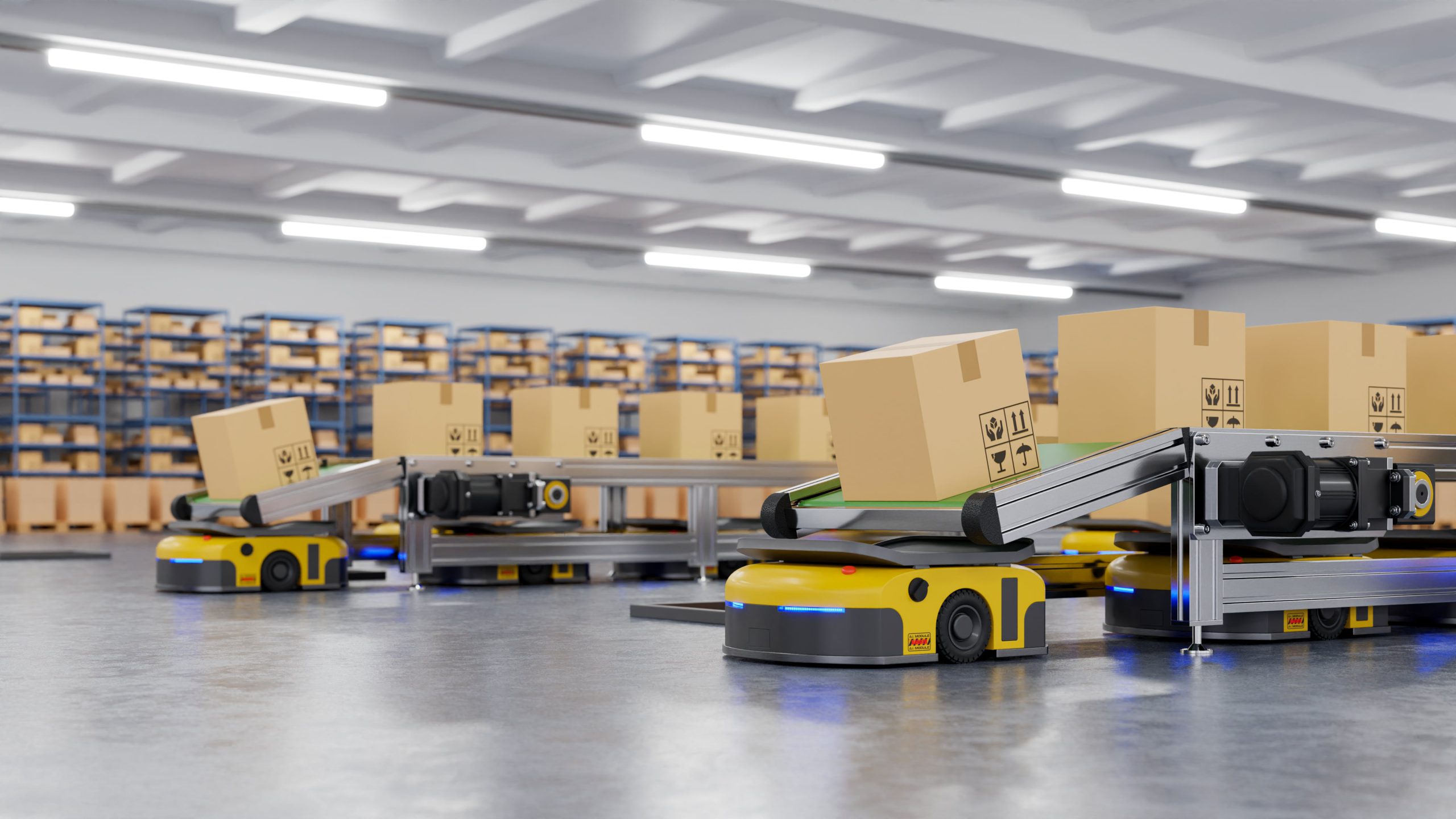
- Store and retrieve products.
- Handle pallets as it is a repetitive and frequent movement: AGV can move pallets from packing pallets to warehouse or shipping docks.
- Automatic loading of trailers: AGVs can take pallets from conveyors or racks and transfer them to trailers according to the specified loading pattern. This is a relatively new use of AGV in the application of a smart warehouse but is becoming increasingly popular.
- Finished product handling: AGV robots move finished goods from the production site to the smart warehouse, or shipping is the final movement of materials before they are delivered to the customer
The latest trends of AGV in smart warehouse
In recent years, businesses have begun to pay more attention to a smart factory, and deployment of the AGV system is also becoming a concern, especially as software and sensor technology have improved. Manufacturers are now offering more precise, efficient and safe means.
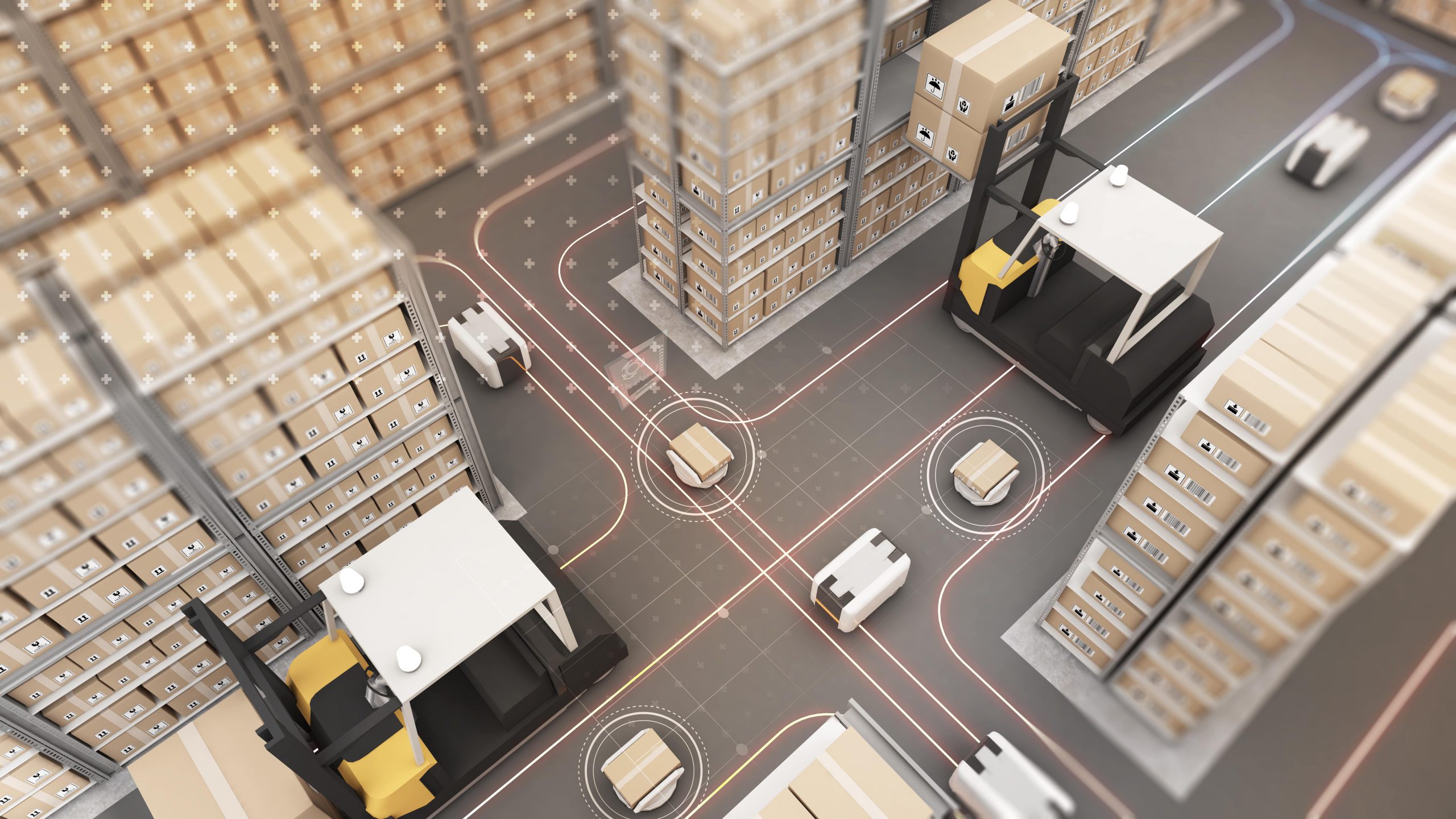
Several types of technologies could have a major impact on the AGV industry over the next few years, including:
1. LiDAR sensor (Light Detection and Ranging)
When placed on an AGV, a LiDAR sensor transmits a collection of laser pulses that measure the range between objects and the AGV. This compiled data creates a full 360° environmental map of the smart warehouse, and the subsequent mapping enables the AGV to navigate throughout the facility without any additional infrastructure.
2. Camera Vision
AGV computer systems and camera-based vision often work hand-in-hand with LiDAR sensors to provide vehicle navigation. The camera’s ability to capture information in real time helps vehicles operate in actual manufacturing and in smart warehouse environments. This data allows vehicles to “see” obstacles and plant infrastructure and, when combined with range information provided by LiDAR sensors, creates a dynamic, complete 3D image of an operational area.
However, the ways in which camera technology can be applied to AGV systems extend beyond navigation. In the future, cameras could improve how vehicles detect pallets, allowing them to interact more effectively inside a smart warehouse system.
3. Dual-Mode AGVs
Dual-mode AGVs, which can be operated manually or automatically, have been on the market for several years already. However, users have often struggled to use these vehicles as designed. Toggling between manual and automatic proved unreliable and ineffective. Nevertheless, with the accuracy and dependability of sensors placed on AGVs continually increasing, the future of dual-mode AGVs will become a new trend in smart warehouse operations application.
4. Software
The software is the backbone of the AGV system in the smart warehouse application. It can address the unique challenges of each installation and thus implement specific solutions to best meet certain applications.
Autotech Machinery JSC. - The leading company of industrial automation solutions in Vietnam
Autotech Vietnam is a leading company in Vietnam in industrial machine manufacturing. Autotech specializes in providing industrial automation solution systems, which includes automation solutions related to smart warehouse, AGV system, Kardex Remstar automated warehouse system – The world’s leading smart warehouse solution.

With more than 10 years of experience in successfully implementing and operating thousands of factories, becoming a reliable partner of many large enterprises in Vietnam such as Samsung, Mitsubishi, Vinfast, Canon, etc, we are completely confident that we can bring satisfaction as well as meet the needs of your business.
Speak to Autotech Experts
Contact Autotech experts to get professional advice for your factory & business.
- Headquarters: No. 11-15, Street 17, Industry – Urban – Service Complex VSIP Bac Ninh, Dai Dong Commune, Tien Du District, Bac Ninh Province, 16000 Vietnam
- Ho Chi Minh City Branch: 49 Street No. 12, KP5 – Hiep Binh Chanh Ward – Thu Duc City – Ho Chi Minh City
- Hotline: (+84) 903 232 625
- Email: info@auto-tech.vn
Find out more about other products/services here: http://www.auto-tech.vn/home-new/en/san-pham/
Connect with us:
- Website: www.auto-tech.vn
- Linkedin: www.linkedin.com/company/autotechvn