CNC technology has gradually become popular and widely used in the mechanical machining industry because of its convenience and superiority compared to traditional machining. The advent of CNC technology has created a new turning point for the mechanical machining industry, opening up new prospects and futures for this industry.

Difficulties encountered in mechanical machining before CNC machining appeared
In the past, when CNC machining technology had not yet appeared, mechanical machining was performed entirely on mechanical machines such as: Mechanical turning, mechanical milling, etc. while the machinery is rudimentary, requiring the person performing the stages to be a skilled and experienced worker. Moreover, the specific characteristics of the industry such as accuracy requirements, etc. have made it difficult for traditional machining in the past to meet the demanding requirements of customers when the market is increasingly constantly changing.

1. Difficult to perform machining on high hardness materials: The nature of mechanical machining in the past was metal removal, taking “hard cutting shoft” to meet the processing of most materials available on the market. However, with the continuous development of the faculty of science and technology, many new materials with higher hardness have been created to meet the needs of the market, so conventional machining methods are difficult to meet the quality and technical requirements set forth.
2. Accuracy and uniformity are not high: The design of the classic machines has many features that support the machining of parts such as levers, cranks, gears, graduated discs, etc. The operator performs the same actions for each part of the same type. However, humans do not have the ability to accurately repeat each movement like automatic machines. Therefore, conventional machining is difficult to guarantee a high level of part consistency. Moreover, operator experience greatly influences part quality and consistency.
3. Special shapes cannot be machined: Previously, metal cutting machines in mechanical machining could only handle regular cuts such as regular circles, ellipses, straight lines, curves, etc. But irregular movements to cut metal according to any curve such as bends, 2D or 3D space, etc. then this machine cannot solve it.
4. Low production capacity: In the past, to machine a product, an operator had to adjust the machine and move each cutting tool, using one or both hands,for precision machining as required. Processing like this is very time consuming and productivity is not high. This also means that the products created will not be much, moreover the accuracy will not be high, leading to low economic efficiency.
5. Unsafe working environment: With the conventional machining method that requires direct human involvement, which mainly performs manual operations, along with rudimentary machinery systems, lack of shields does not ensure safety during human operation. Moreover, the movement of working equipment, means of transport, etc. are activities that take place frequently in the machining process, which can lead to problems such as metal splashing, cutting through, clamping, etc. If a little carelessness in the process of working, it can cause problems with different levels of injury, unsafe in mechanical machining for workers.
Advantages of CNC machining compared to conventional machining
Mechanical machining with CNC technology allows us to eliminate all uncertainties. This technology has brought a breakthrough in automation technology that makes all the difficulties in mechanical machining before it will be solved. CNC machining is a modern machining method, so it possesses many highlight advantages compared to conventional machining methods.

1. Reduce machine setup time, preparation time: Once the program of precision machining has been written and proven, it can be completely reused by the operator in the future. Although the preparation time for the first machining is usually longer, it is completely negligible in the second machining. Even if a technical change of the part requires modification of the program, it only takes a short time, thus reducing preparation time.
2. High accuracy and repeatability: The precision of CNC machining is almost absolute, the mechanical error is extremely small, helping to ensure uniform product quality. The process is more precise than conventional machining and can be repeated in the same way many times. Besides, any program stored on disk or on computer memory is customizable, but once proven, usually does not need to be changed. The program can be reused as many times as you want without losing data.
3. Increase production speed and productivity: Computers are used to control the automation of machines and processes, thereby increasing production speed and quality. CNC machining machines work automatically, continuously and with little downtime, thus greatly reducing production time and increasing machine working time. Moreover, CNC machining machines produce high-quality products so there is no need to use the machine to check.
4. High flexibility: CNC machining can both process small, single parts and can be mass-produced quickly in any size, shape or texture when required. Most importantly, machining programming can be done outside the machine through computer devices and various programming programs.
5. Safe working environment: One of the main advantages for CNC machine operators is safety. Using a CNC machine is much safer than a manually operated machine because the operator can control it remotely or even have a safety door that closes throughout.
6. Cost savings in the production process: Compared with conventional machining, CNC machining is much more economical. Since minimal operator involvement is needed to manage the CNC process, a single operator can oversee multiple machines at once with high degrees of accuracy and precision, which reduces labor costs.
The combination of high speed, efficiency, accuracy and fewer employees will create better profits for the business. Companies can then use lower costs to create competitive advantages and business reinvestment opportunities. Saving money or making more money is one of the common benefits of CNC machining.
How has CNC technology changed the mechanical machining industry?
The mechanical machining industry had a remarkable turning point when CNC machining technology appeared (Including CNC turning and CNC milling). This method does not require direct human involvement as in conventional machining. Machining by numerical control does not require graduated discs, levers, handwheels, etc. Once the detailed program has been proven, it can be used an unlimited number of times, always resulting in consistent results.
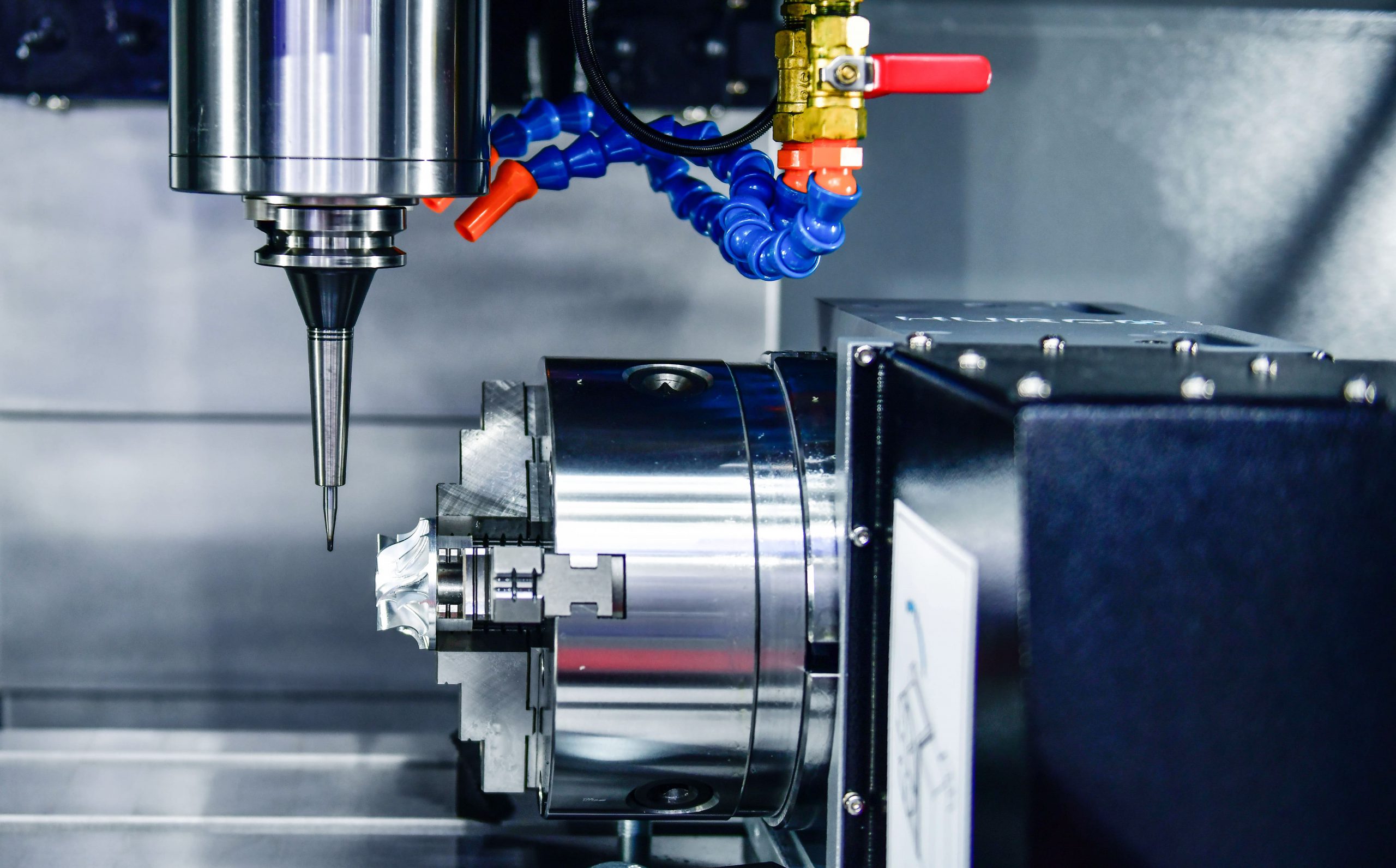
Besides, when using the machining method by CNC technology, complex mechanical parts are performed. The principle of the CNC machine is the application of CNC plasma cutting to the application of metal cutting, stainless steel grooving, metal, 3-dimensional samples are also sculpted by CNC drilling technology.
Moreover, if in the past, metal cutting machines could only perform basic, monotonous patterned cuts such as circles, ellipses, curves, etc., and more complex and sophisticated cuts cannot be solved, but with CNC technology, when you want to cut in a circular shape, a curved line, or any shape, it becomes easy. Programming CNC technology is quite simple, just use the computer to draw the figure that needs to be cut through common software (AutoCAD, corelDRAW, etc.), then issue the working commands, the machine will cut exactly as required.

These are really new steps to improve both aesthetics, quality and versatility in the mechanical machining industry.
Applications of CNC machining in industrial manufacturing
Currently, there are many industries that have used mechanical machining by CNC technology, of which the most special is the field of machine manufacturing. Operators can use CNC technology to process different types of products from wood to stone and metal.

- In the field of furniture manufacturing, CNC machining technology is used to process patterns and carve details quickly.
- In the fields of manufacturing household appliances and assembling vehicles, CNC technology is also used to process molds, for sophisticated designs.
- In the field of mechanical engineering, CNC cutting machines are used to cut complex shaped metal plates with absolute precision. The CNC torch still used is oxygen gas cutting, plasma cutting and more advanced than laser cutting.
Autotech Machinery JSC provides optimal solutions for CNC machines
Mechanical machining is a heavy job in the working environment with the smell of grease that affects the health of workers. Therefore, large companies want to build automation systems in manufacturing to reduce personnel at this stage.
Understanding these difficulties, Autotech Machinery JSC offers businesses the optimal solution for CNC machine systems, including parts supply for CNC machines as well as automatic workpiece feeding system for milling machines, thread rolling machines, grinding machines, broaching machines, sheet metal working machines, etc. helping automate the workpiece feeding and taking stages, thereby, it has improved manufacturing productivity as well as reduced costs in large-scale production.

With a team of high quality and experienced engineers, becoming a reliable partner in the field of mechanical engineering for big customers such as Samsung Display, Mitsubishi, Vinfast, etc. we are confident, ready to provide and support the CNC tending solution system as well as the automation solution system to each customer in the fastest time with the most optimal solution.
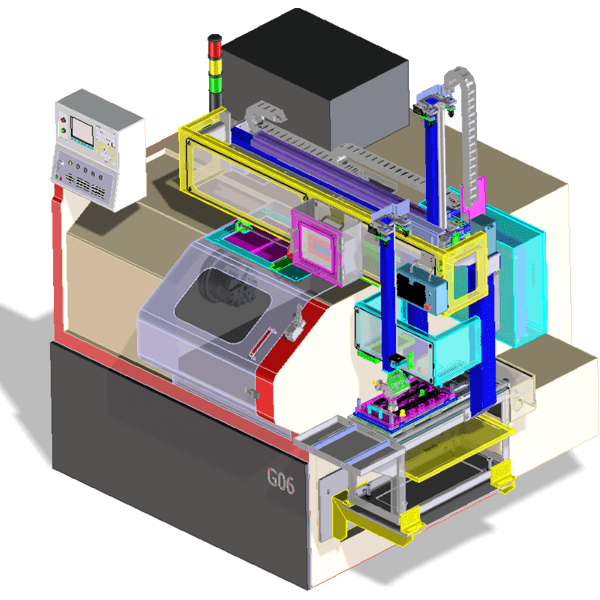
Customers coming to Autotech will be advised on appropriate CNC tending solutions as well as guaranteed the quality of machining orders with high accuracy, good price and always meet the progress of your business.
Speak to Autotech Experts
Contact Autotech experts to get professional advice for your factory & business.
- Headquarters: No. 11-15, Street 17, Industry – Urban – Service Complex VSIP Bac Ninh, Dai Dong Commune, Tien Du District, Bac Ninh Province, Vietnam
- Ho Chi Minh City Branch: 49 Street No. 12, KP5 – Hiep Binh Chanh Ward – Thu Duc City – Ho Chi Minh City
- Hotline: (+84) 903 232 625
- Email: info@auto-tech.vn
Find out more about other products/services here: http://www.auto-tech.vn/home-new/en/san-pham/
Connect with us:
- Website: www.auto-tech.vn
- Linkedin: www.linkedin.com/company/autotechvn