Smart factory is a typical result of industrial 4.0, ushered in a new era for the manufacturing industry. One of the breakthrough technologies that has created a major turning point that completely changes the traditional processes, production methods and management, is the mark of the smart factory. The industry now takes on a more advanced, optimal and modern form. So, what is a smart factory? Read the article below with Autotech to have a more overview of the smart factory!
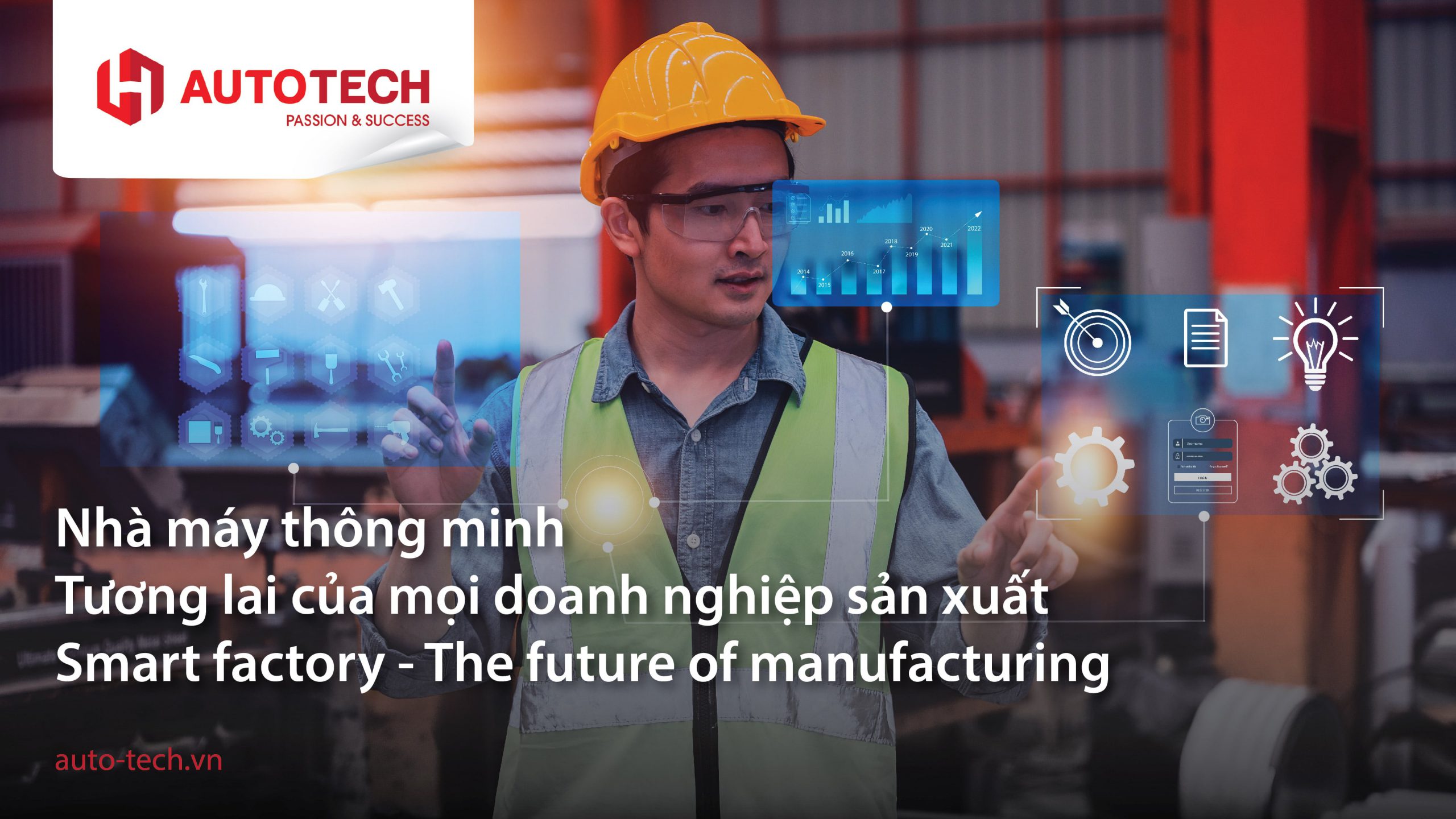
Overview of Smart Factory
According to the historical process, it can be seen that the smart factory goes through the following stages:

1. Smart factory in the 1.0 industrial revolution
This is the stage of mechanization: Smart factories in this period operated mainly by using steam engines and mechanical machines to replace some human work. The application of these achievements has increased production efficiency by 4 to 8 times.
2. Smart factory in the 2.0 industrial revolution
This is the stage of electrification and mass production: The highlight of smart factories at this stage is the large-scale production with mass production lines, the appearance of many large factories in many fields such as phones, cars, airplanes, etc. Moreover, electricity and electrical appliances are put into the production system, thereby creating a premise for the outstanding development of advanced automation technologies such as production lines, lighting equipment, electric heating equipment, etc. in this period.
3. Smart factory in the 3.0 industrial revolution
This is the phase of digitization and integration of automation: The highlight of smart factories at this stage is the automated machine system under computer control with pre-written programs (programmable). Computers and application software gradually become indispensable tools in every factory from design, planning, production organization to data storage, information processing, payment, communication, etc. The role of humans lies in managing those automated machines and connecting them with each other.
4. Smart factory in the 4.0 industrial revolution
Inheriting the achievements of smart factory 3.0, the 4.0 technology is the stage of connectivity and smart manufacturing. This stage marks the birth of the smart factory – a leap forward, creating a new milestone marking a complete change in the automation of production in the future. Production plants are raised to a new level, automated production systems along with modern technologies (CNC machines, robots, cameras, sensors, etc.) are able to connect with each other to information exchange and decision making.
What is a Smart Factory?
As defined by Deloitte Insights, smart factory solution or factory 4.0 enables a traditional automated production system to turn into a system that is connected and has continuously collected business data so that the system can learn and adapt to the changeable demands of the market. As a result, it leads to more efficient & flexible operations, reduced downtime, predictability, and adaptability.
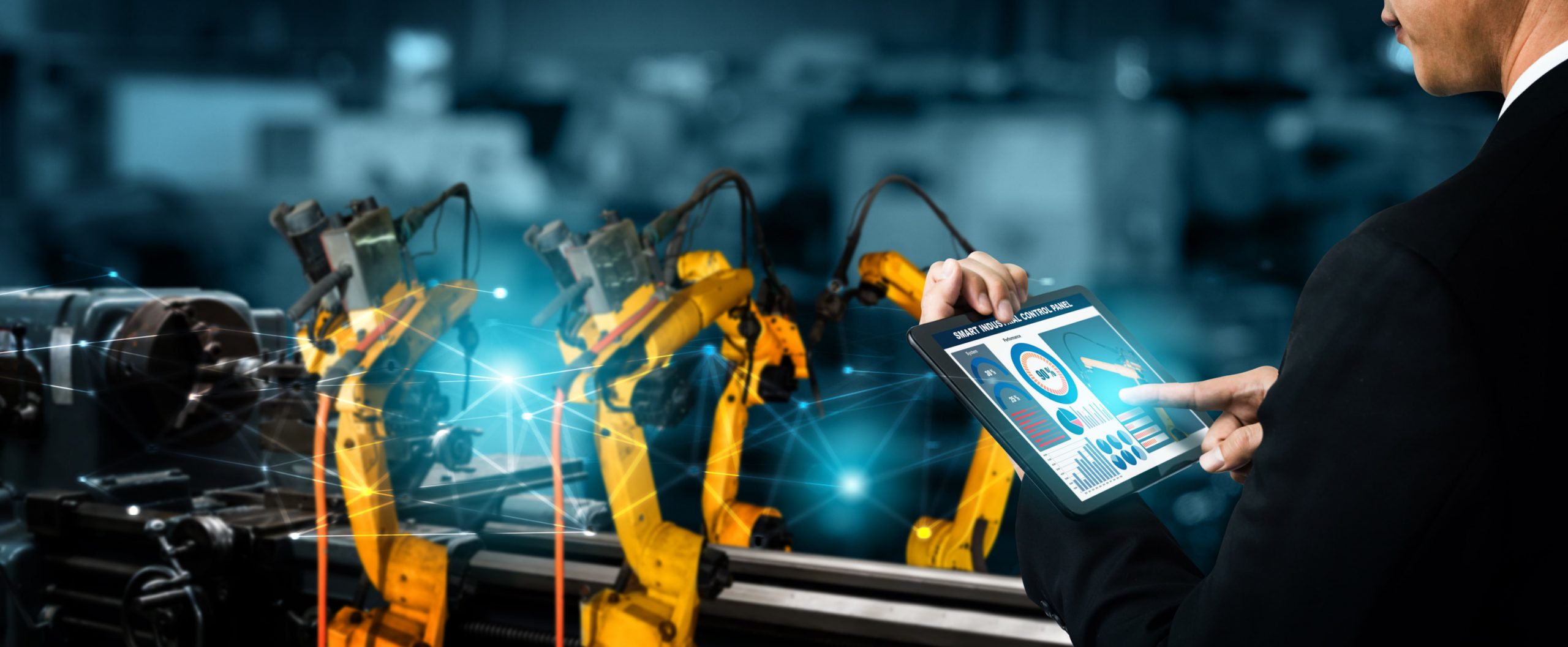
In other words, a smart factory is a digitized and highly connected production facility based on smart manufacturing.This factory is built based on modern business management systems such as MES, ERP combined with modern technology systems (AI, IoT, big data, …) to support human control and operate all production activities.
Smart factory is considered a great step forward and a breakthrough result of industrial 4.0 compared to the previous 3 revolutions, creating a great smart factory project in industrial production. The emergence of the smart factory has created a highly competitive market, promoting the development of industries, and opening up many development opportunities for many businesses in the future.
Benefits of factory 4.0

1. Higher productivity
Thanks to the automation of the entire production process, the smart factory can operate 24/7, so the production process is accelerated, limiting human intervention in the operation of the factory. That makes the process faster and cheaper.
2. Better cost optimization
The smart factory is integrated with an intelligent automation system, helping the production process to operate independently, limiting human intervention in the process, thereby helping businesses reduce redundant processes and ensure consistent production at lower costs, while reducing resource waste.
3. Higher customer satisfaction
Smart factories have the ability to collect valuable information through IIoT platforms to help businesses easily assess and analyze customer needs and overall behavior in order to create suitable products with higher requirements of customers. This helps businesses increase customer satisfaction even when there are many competitors in the same industry.
4. Better product quality control
Powered by automation technologies and advanced digital systems, smart factory solutions help to quickly detect problems and identify the cause of failures. Therefore, reducing the rate of waste and lead time, while increasing productivity and product quality. Moreover, it also helps the operator to have timely solutions to fix errors.
Technologies used in smart factory
Smart factories use a variety of different technologies related to the fourth industrial revolution (Industry 4.0) to optimize smart manufacturing processes. These technologies include:
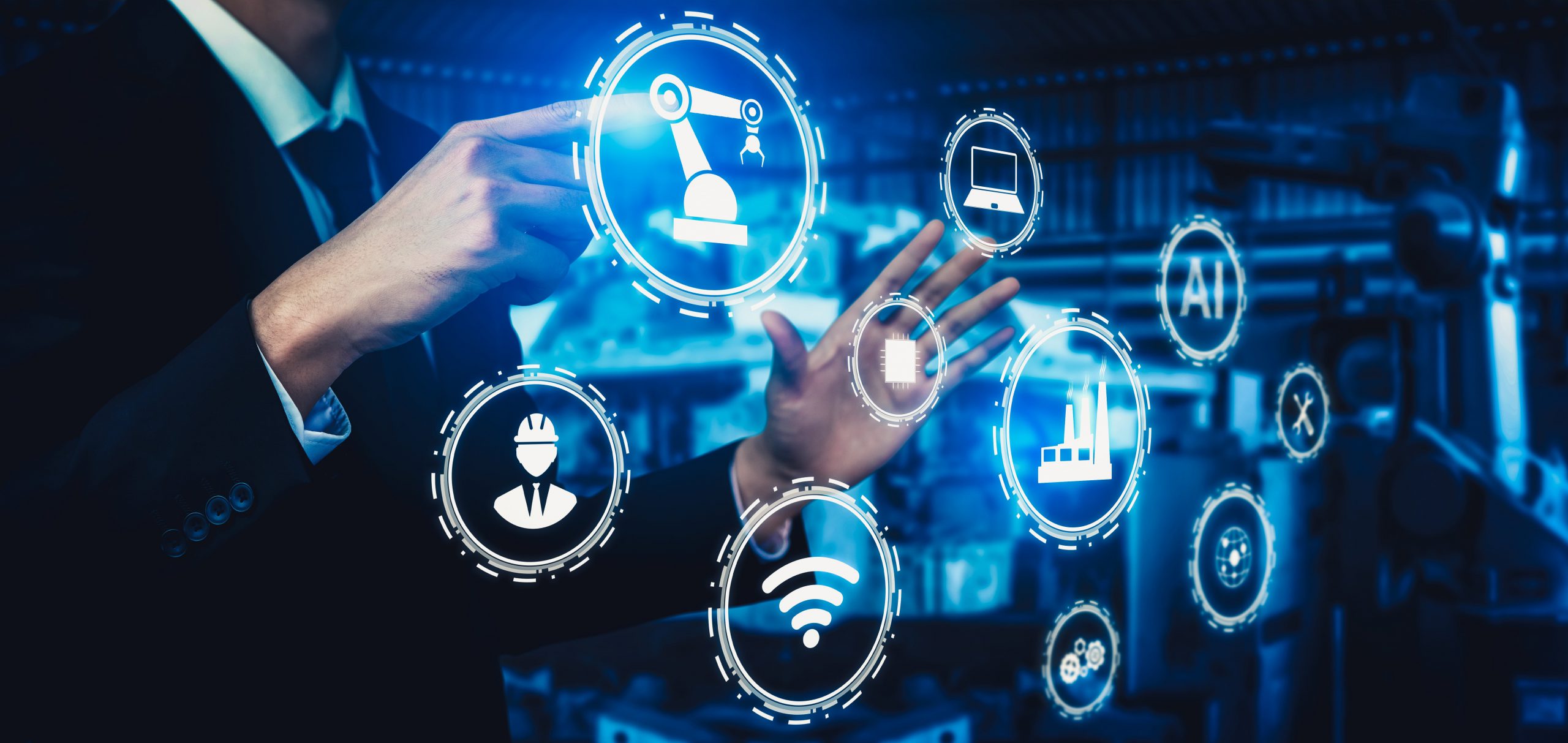
1. Cloud Computing
This is where the smart factory can store all the information and the large volume of data that is generated both in the plant (robots, sensors…) and in the specific tools (MES, ERP…).
2. Digital Twins: Increase efficiency, control and operations planning
Digital Twins help create a replica or concept of a production process in a smart factory. 3D simulations are generated with large data sets through the system’s sensors, thereby allowing operators to have a better overview of processes, thereby helping to analyze, control and plan future activities.
3. Sensors: Monitoring and data collection
In a smart factory, all machines and assets are installed with smart sensors to help the system access data continuously, ensuring that the data is continuously and fully updated to reflect current status. Sensor technologies are the smart factory platform as it can monitor and track all the processes and equipment in the factory and enhance the exchange of information in real time. Therefore, sensor technology is the backbone of the smart factory that improves the agility, safety and efficiency of the production process.
4. Big Data: Analysis, prediction and support make decision
All information of the smart factory is generated through connections between automation machines or plants and tools must be collected and analyzed in real time with the goal of optimizing the entire production process. Big Data is responsible for processing large volumes of data and supporting administrators to make decisions in the most reasonable time.
5. Artificial intelligence (AI): Increase operational efficiency without human intervention
Artificial intelligence enables the smart factory to operate and improve manufacturing processes faster based on learning through data collected from different devices and processes. AI is supported by many automation technologies that enable smart factories to achieve high productivity and optimize operating costs.
6. Industrial Internet of Things
Industrial Internet of Things (IIoT) connects all the machines and devices used in smart factories that are linked by data communication systems on the internet. Using IIoT devices allows for the exchange and use of data between people and machines so that operators can coordinate systems, capture data, control production remotely, and exchange information between the system and the product. IIoT devices enable operational efficiency, control, and visibility over different stages of manufacturing.
7. Cybersecurity: Smart factory data protection
Cybersecurity is an essential technology in a smart factory since privacy and data protection is the most key aspect for industries.
8. Robot: Process automation
Robots facilitate those tasks that require a high level of accuracy or all those that are repetitive at smart factories. Each activity to be developed will require a cognitive robot or an autonomous robot, or even both.
Steps to build a smart factory
Smart factory implementation requires the involvement of many resources. Therefore, businesses need to determine the steps to take to achieve the highest efficiency, in accordance with your business needs.

Step 1: Smart factory model positioning and orientation
Each enterprise, each factory has its own difficulties in the production stages. Therefore, it is necessary to determine what level your factory is at the very beginning of smart factory implementation. This job is strategic, to do requires business to have a long-term vision, carefully analyze the factor of opportunity and threats, and at the same time must have a certain potential and determination.
Step 2: Smart factory problem identification and improvement methods
Not every modern tool is absolutely necessary or suitable for your plant. In manufacturing, to build a smart factory, it is necessary to identify production problems, and to have methods to solve them. And technology is the tool in the methods, tech-savvy people will choose the optimal methods to solve these problems in the most efficient way.
Step 3: Smart factory solution provider
It can be said that the role of people is extremely important, to come up with a solution for a smart factory, it not only requires people who understand production, have knowledge about production improvement, and not indispensable is technology capacity.
In addition to the 3 main steps to build a smart factory, there are other steps such as survey, analysis – design – programming – testing, installation, testing (Golive), system deployment and acceptance. But these steps can be reduced if in step 3, you choose a company that specializes in providing leading industrial automation solutions, accompanying your business to build smart factory solutions. Autotech Machinery is a leading automation company in Vietnam that brings modern technology solutions to factories. Let’s learn about Autotech Machinery JsC. below.
Autotech - The leading automation company in Vietnam
Autotech Machinery is currently one of the leading industrial machine manufacturing companies in the field of automation in Vietnam, having successfully deployed and operated digital solutions in industrial machine manufacturing projects, upgrading and improving automation lines for many corporate customers in Vietnam such as Samsung, Canon, Mitsubishi, Vinasoy, etc.
With experience and available advantages in the field of automation, Autotech Machinery, we are confident to accompany your business to start the journey of building a smart factory by providing digital solutions such as smart warehouse solutions, manufacturing, automation line improvement, robotics, … are supported by a team of experienced engineers.
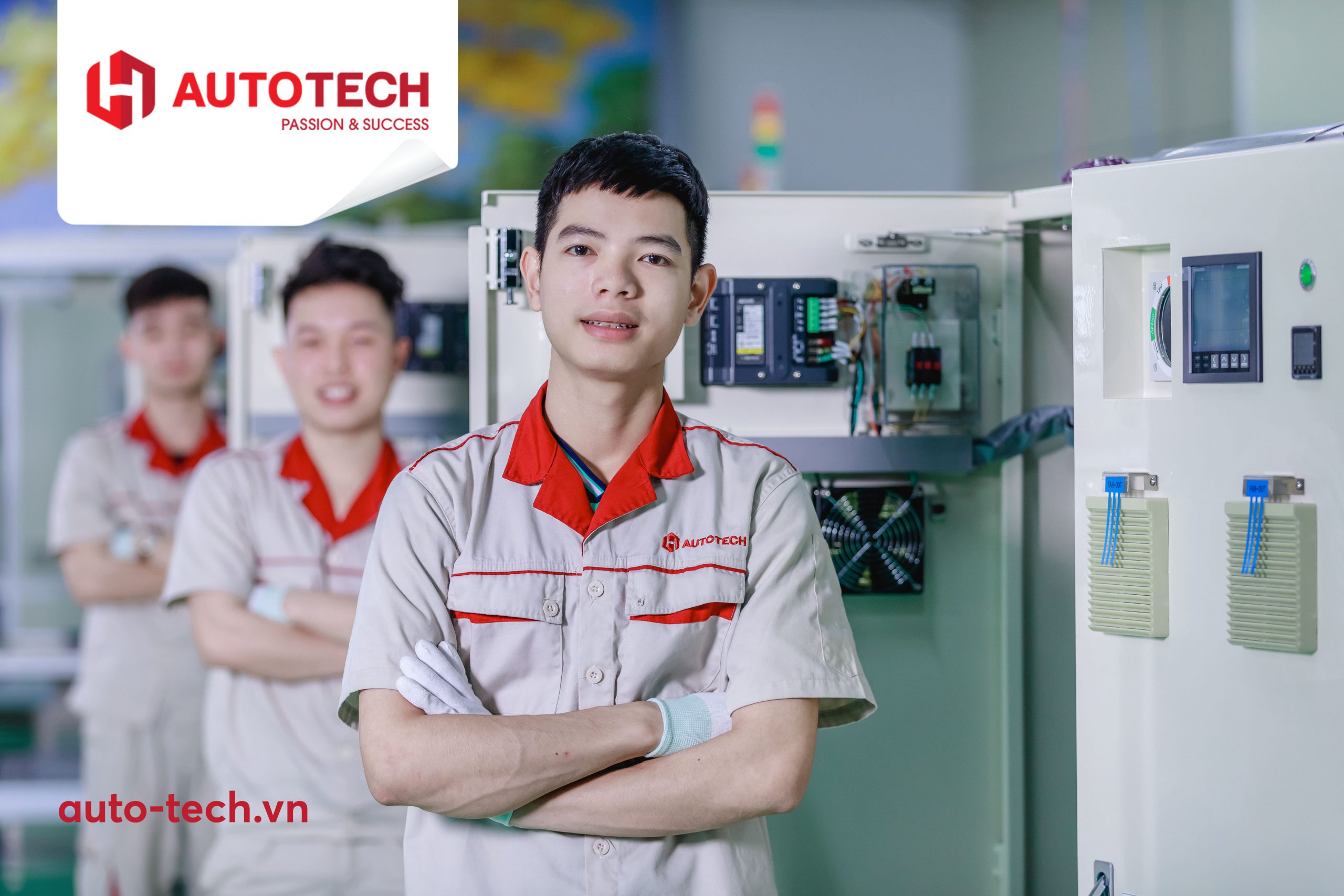
If your business does not know where to start building a smart factory, please contact Autotech Machinery for advice on the optimal automation solution suitable for your business.
Speak to Autotech Experts
- Address: No. 11-15, Street 17, Industry – Urban – Service Complex VSIP Bac Ninh, Dai Dong Commune, Tien Du District, Bac Ninh Province, 16000 Vietnam
- Hotline: (+84) 903 232 625
- Email: info@auto-tech.vn
Find out more about other products/services here:
http://www.auto-tech.vn/home-new/en/san-pham/
Connect with us:
- Website: www.auto-tech.vn
- Linkedin: www.linkedin.com/company/autotechvn